Главный офис
в центре Европы
Гарантия
до 24 мес
до 24 мес
Лучшие
цены
цены
Экономия
от 15 до 55%
от 15 до 55%
Доставка
по России
по России
Все грузы
застрахованы
застрахованы
Бесплатная
доставка
доставка

Alfa Laval U-Turn
Категория - Холодильные системы
Официальный сайт Alfa Laval (Швеция) :
www.alfalaval.com
Узнать цену
В нашей компании вы можете выбрать и купить Alfa Laval U-Turn, а также другие запчасти от
компании Alfa Laval с доставкой по всей России, в том числе в ваш город : Дублин. Для запроса цен, сроков поставки
и других характеристик продукции Alfa Laval, пожалуйста, заполните форму обратной связи или пришлите описание необходимых Вам наименований
на электронный адрес info@famaga.ru
Описание
Продукция, изготовленная шведской Alfa Laval компанией, подходит для использования в пищевой, химической, фармацевтической, горнообрабатывающей и нефтяной промышленности.Преимуществом товара является длительный срок службы без необходимости осуществления регулярного обслуживания, а также его первоклассное качество и надежность. U-Turn is a liquid separator especially designed for use with plate heat exchangers in ammonia applications. The module – including the separator and plate heat exchanger ensures minimum pressure drop losses and maximum energy efficiency. Alfa Laval U-Turn is designed to utilize the very best from Alfa Laval’s plate heat exchanger technology. Installed above, the self-contained U-Turn can be easily mounted onto the compatible plate heat exchanger. It can cover ammonia capacities from 200 to 1400 kW at 0°C evaporation temperature and from 50 to 500 kW at -40°C evaporation temperature. The module provides an effective and compact installation with less vertical rise and smaller overall dimensions than any other solution. Main design features- Compact dimensions
- Shorter height and length allowing installation onsite without dismantling
- No additional support is needed, as the U-Turn separator is supported entirely by the plate heat exchanger
- Easy maintenance, as both sides of the plate heat exchanger are fully accessible.
- All ammonia connections access the same side which makes installation easy
- Integrated oil drain
- Stainless steel ensuring corrosion resistance and no need of surface treatment
|
Пригласить на тендер
Наш менеджер свяжется с вами в ближайшее время.
Запрос отправлен
Запрос отправлен
Письмо не отправилось
Письмо не отправилось
Оставьте заявку
Мы свяжемся с вами и ответим на любой возникший вопрос.
Запрос отправлен
Запрос отправлен
Письмо не отправилось
Письмо не отправилось
Заказать звонок
Мы ответим на любые вопросы и поможем оформить заказ
Спасибо за вашу заявку!
А пока мы обрабатываем ваш запрос, вы можете найти другие необходимые вам позиции - ведь в нашем каталоге более 10 000 брендов!
Заказывая у нас сразу несколько позиций вы существенно экономите на доставке!
Каталог производителей
Искать
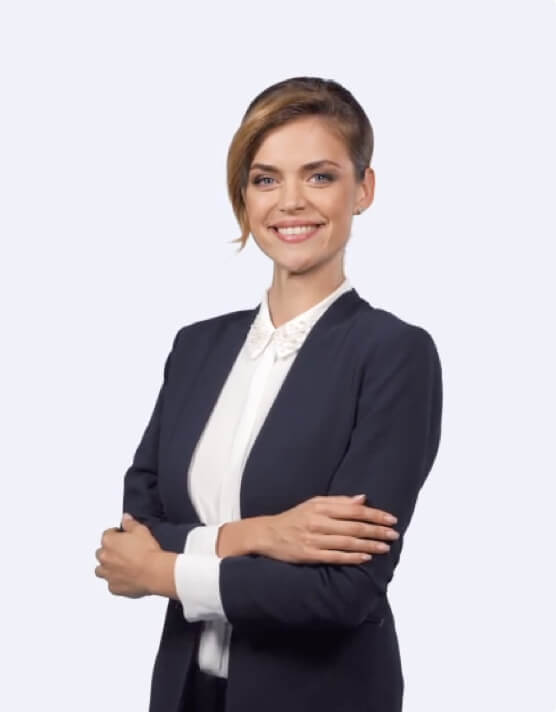
Что-то пошло не так
Кажется, что-то пошло не так. Попробуйте повторить попытку ещё раз позже.
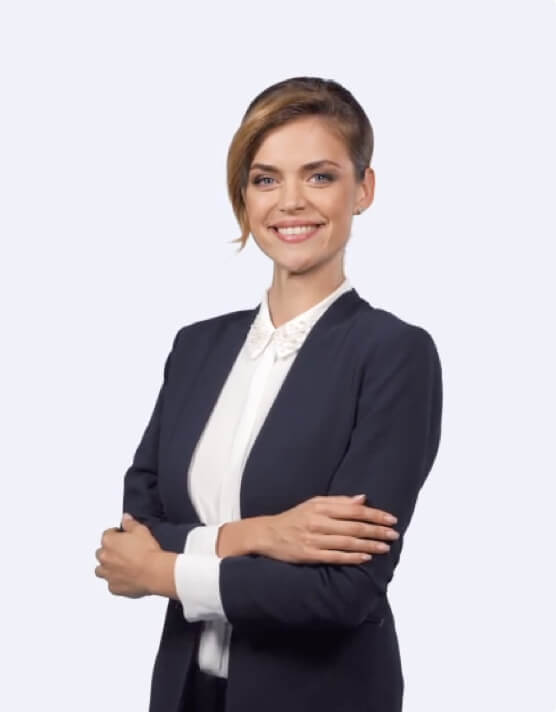